We live in a world where technology supports us in whatever we do. And woodworking is no exception to that. Technology helps us to get faster and more accurate results, takes a lot of guessing out of the equation and, ultimately, makes the whole process less subject to mistakes, thus saving bucks in our pockets.

But…is this entirely true? Because when we talk about woodworking, we traditionally refer to an art that has been there for thousands of years and has always required a set of skills that no machine or computer will ever be capable of replacing completely.
So, here are the 5 most important skills every woodworker should have and strive to improve daily.

Wood is a hygroscopic material that moves relative to the external moisture content. This is a fact, and we have to live with it.
Sure, you experienced at some point in your life a cabinet door that was not closing as well as it used to or a drawer that now is stiff and requires some force to come out.
This is because the wood has cells that absorb and release water, thus expanding and shrinking the board as it exchanges moisture with the environment where it is placed.
And if this is not enough, every species reacts to moisture differently, either relatively stable or more susceptible to minor changes.
Generally, wood moves the most across the grain and has negligible movement along the grain. Therefore it is important to know how to select, mill and join boards together so that, as moisture changes, the stability and integrity of the piece will still be preserved.
As an example, here is how you can calculate how much a board will move with the moisture change; The process is relatively easy and follows four simple steps:
a.Measure your board width.
As we said, wood moves more across than along the grain, and the narrower the board, the less the movement will be. That’s why some industrial furniture makers (did I say IKEA?) make products with thin strips of wood, as this dramatically reduces the chances of movement.
b.Find the average moisture content change (MC)
Loof for the MC change in the environment where the wood will be put. This doesn’t have to be an exact value, considering that climate-controlled houses average a 3 to 4% change per year.
c.Determine the dimensional change of the species you are going to use.
The formula works for moisture contents between 6% and 14%, the common furniture range. For example, with a flat-sawn board of white oak, the value is 0.0365.
d.Do the math.
Multiply the width of the board by the annual moisture change. Then multiply the result by the value relative to the species.
Here is an example:
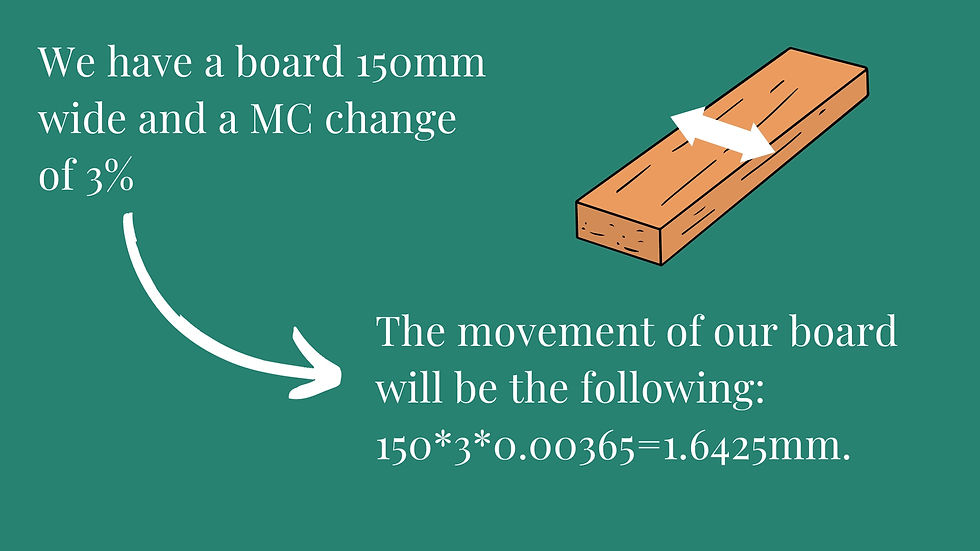
If the same board of White Oak would be quarter sawn, the seasonal movement would then be 150*3*0.00180=0.81 mm, i.e., half the movement of a flat-sawn board!

Ask any woodworker, and he or she will tell you that a well-sharpened tool will deliver you faster and more accurate results.
There's a popular story about Abraham Lincoln, one of the most important presidents in American history. Before becoming President, he was a woodcutter and, once questioned about his superior skills, he said:
Give me six hours to chop down a tree and I will spend the first six sharpening the axe.
Sharpening your chisels and plane blades can look daunting, but once you understand the basic principles, it will become a quick and satisfying routine that should be followed regularly.
Just give yourself some time to master this skill, and you will see woodworking with hand tools as one of the most rewarding parts of the construction process.
So, why is it so intimidating? I'm not sure I have the exact answer to this question; there might be several reasons that affect each of us at a different level.
When I started my journey into woodworking, I saw the sharpening process as the most difficult part, probably because I was unsure of the exact sequence. I was so afraid of spoiling the blade or changing its original angle.
I would look for sharpening guides and foolproof methods to avoid mistakes. Still, the thing was, I just needed some exposure to the practical part, and somehow, I had to ignore the hundreds of different methods I had watched on YouTube.
Sharpening is much easier than you think, so why complicate it?
Let’s see here some basic principles of sharpening:
Regarding chisels, the bevel angle is between 25 to 30 degrees.
You need to know a very important thing: No chisel or plane blade will come to you ready to use!
Manufacturers produce chisels that need final tuning that can only be done on a sharpening stone. The brand doesn’t matter; they will eventually need some final touches. How much will depend on the quality of the product, and some chisels and blades will come out of the box, almost ready to go.
The first and most crucial part is flattening the back. Once properly done, it will serve you well for a long time before you return to it.
To do this, you want to start rubbing the back of the chisel on a wet stone with a coarse grit, and 220 grit is a good start. If you want to be sure that the stone is dead flat, invest in a diamond stone, it will give you consistent, repeatable results, and you will also use it to flatten all the other stones.
As you progress, check the back of your chisel for consistent scratch patterns, and once it’s reasonably flat, move to the next stone with a higher grit. A good set of stones follows this increase in grits: 220, 1000, 4000, 8000, 10000+
Continue with this procedure until you get a mirror-like surface.

Then, move to the bevel. You can keep the standard factory bevel of 25 degrees or increase it to 30 degrees. As for the back, start from a 220-grit stone and move up to the finest grit you have available.
The secret in sharpening is to intersect the flat back and the bevel to form the acute-angled wedge with its sharp cutting edge.
In a future post will dedicate more time to explaining how to get a scary edge on your chisels and plane blades.

Hand tools occupy a very important part in woodworking, and even today, where technology seems to overtake manual activities, the use of a handsaw or a chisel remains unsurpassed. Not considering that, in the collective imagination, the hand-cut joinery and finishing remain one of the most "romantic" parts of working with wood.
Even if nowadays there are woodworkers that can make any kind of project from A to Z with the sole use of machines and power tools, there are many reasons why it is still important to learn how to use hand tools, at least the most common ones.
a.they get the job done faster
Believe it or not, it's exactly like this: in many situations, a hand tool can get you done faster than a machine.
Yes, because a machine or a power tool requires to be set before they can deliver a precise result, whereas the hand tool is there, ready to be used.
Let's take a simple example where you want to cut a mitre joint (where the two parts are cut and joined at 45 deg).
You could go to the table saw, measure and set the angle at exactly 45 deg, and cut the wood. This operation could probably be very efficient if you have to cut several pieces because, with just one setting, you will have repetitive, consistent cuts.
But what if you need only one cut? It would probably be faster to get your hand saw, mark and scribe the line with a combination square, and cut and refine your cut on a shooting board.
b.they accomplish unique tasks
The efficiency I just described becomes even more evident in front of unique situations where the machines would require laborious settings or would simply not be appropriate for the kind of task.
I will give you an example. When I built my first piece at school, the Desert Flower, I decided that the main carcass would be dovetailed on the four sides and that these dovetails would have a specific pattern (call me crazy...)
I didn't have a dovetail template for this kind of pattern, and it would cost me too much to buy one for what I needed to do. On top of that, I wanted to enjoy the process of hand-cutting...so I went for the hard way. The result is visible in the picture, and I couldn't be more proud.

c.they create less fine particles
Hand tools create much less dust and fine particles in the air compared to power tools and machines. And also much less noise.
This is because they operate at a lower speed, like a hand saw, or remove bigger chips from the wood, like in the case of a chisel or a plane.
When you hand woodwork, you generally don't need to wear a mask with a filter, and the process becomes more pleasant and less stressful.

There are countless different joints you can find in woodworking. Some of them are structural and specific to some specific needs, while others are primarily aesthetics and will make your furniture shine among others.
You will often hear that you can achieve the same result in ten different ways in woodworking. This is particularly true for joints as you can make them using different sets of tools, from the traditional way with hand tools to the more modern techniques that machines and power tools, up to computerized numerical controlled machines (CNC).
Here are the most popular wood joints:
a.mortise and tenon
As a general description, the mortise describes a pocket cut into a piece of wood, and the tenon is a corresponding positive part on the end of another piece of wood that fits into the mortise.
The tenon has shoulders that are mostly cut at 90 degrees and sit against the face where the mortise is cut, providing strength and structure while preventing tipping or racking out of the square.
b.dovetail Joint
Probably the most sought joint ever and a sign of raffinate techniques, this joint offers incredible strength in joining the two parts. Recent studies report that a well-made dovetail joint unglued is as resistant to failure as much as a glued joint.
Tradition wants this joint cut with hand tools as it offers flexibility on where pins and tails are positioned. Nowadays, many jigs on the market allow you to create this joint fast and accurately.
c.box joint
This joint is a simplified version of the dovetail joint and is generally easier to make, most of the time using a jig on the router table or the table saw. To understand it, think of two hands with straight fingers interwoven.
d.butt joint
The simplest joint of all, it is also the weakest as it connects the ends of two pieces of wood. You can use it to connect the four sides of a simple box but to make it more resistant, and you may want to use dowels that reinforce the connection between the two pieces.
5. KNOW HOW TO APPLY A FINISH

How many times have you admired a beautiful piece of furniture and noticed its shine or matt finish? This is something that highly contributes to the style and final result of the piece.
So, you might think that the main purpose of applying a finish to wood is to enhance its beauty and reveal its personality; this is partially true, as a correctly chosen and applied finish has the magic power to highlight the grain and create a beautiful contrast.
But there is more.
As we saw at the beginning of this post, wood is a hygroscopic material that constantly exchanges moisture with the external environment.
A wood finish seals the cells in the wood and limits this moisture exchange, with the ultimate benefit of reducing seasonal wood movements.
This means that an untreated piece of wood will move more than a finished one!
Several techniques are used to finish wood, and nowadays, as we move to a greener environment, oils are extensively used as they are easy to apply and food safe.
Among the popular ones, it’s worth mentioning brands like Osmo or Rubio Monocoat that offer a wide range of choices in colours and final effects.
CONCLUSION
In this post, I gave you an overview of the 5 most important skills that every woodworker should have and why it's worth investing in improving them.
Some of them, like understanding the behaviour of wood or learning how to sharpen your tools, might look daunting for a beginner, but I encourage you to put a minimum effort into learning and don't give up. The result will be well worth it.
Woodworking is magic and can also become addictive :-) It's that kind of addiction that I recommend to everyone as it produces happiness and peace of mind. Try to see it!
If you love woodworking as we do, join our community by subscribing to our mailing list. All our latest news and fresh new blog post are in your mailbox every week.
Dubai Makers Society offers a woodworking space to rent using power tools and heavy machines.
We also run regular classes for those who want to learn woodworking.
Comments